NSDT工具推荐: Three.js AI纹理开发包 - YOLO合成数据生成器 - GLTF/GLB在线编辑 - 3D模型格式在线转换 - 可编程3D场景编辑器 - REVIT导出3D模型插件 - 3D模型语义搜索引擎 - Three.js虚拟轴心开发包 - 3D模型在线减面 - STL模型在线切割
如今,研发团队越来越多地转向系统级数字孪生来开发、改进和分析其设备和流程,尤其是在结构、流体和电磁领域。
但是,采矿业在散货流转应用方面没有这样的机会,尽管它面临着类似的要求:减少停机时间,更好地预测维护,调整效率,提高产量和提高安全性。
ANSYS和Rocky DEM软件公司已经开发出一种利用机理、实验设计和离散单元建模(DEM)工具为采矿、散货和加工行业创建数字孪生的方法。
此解决方案使用降阶模型 (ROM),可最大限度地降低计算成本/时间,同时准确预测实际操作。
除了财务和效率优势外,数字孪生还为该行业提供了改善其安全记录的机会。
通过自动化,公司可以降低散装物料搬运机的风险;最小的设备破损(更好的维护计划的结果)意味着更少的工人受伤。
1、数字孪生体工作原理
为了提高计算效率,基于物理的数字孪生从基于全 3D 物理的 ROM 开始。它们通过输入传感器数据的物联网(IOT)平台连接到真实的现场资产。
由此产生的数字孪生提供了无法测量的其他数据。
无需参考或依赖历史数据,数字孪生已被用于通过模拟产品组件来加速产品研发,识别和排除潜在的过程问题,以及预测/提高产品性能。
ANSYS产品为构建数字孪生提供了强大的功能。对于采矿业应用,仿真还引入了 Rocky DEM 降阶模型。
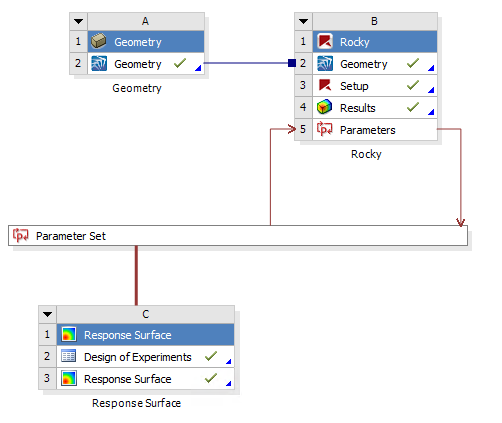
这些ROM通过使用快速评估来估计连续空间中的行为,而不是进行完整的物理求解。此外,Rocky DEM还集成到ANSYS工作台™和参数环境中,从而简化了分析过程。
2、采矿业案例研究
在这个真实的采矿测试案例中,穿梭车将开采的煤炭从岩石表面运送到进气给料机。原材料被倾倒到输送机上,输送机将其输送到位于进气口下游的破碎机构。
当矿车倾倒负载(有时太快)时,溢出物无意中发生并积聚,影响下一班班车可以停放卸载的位置。
当多个穿梭车同时卸载时,沿输送机的质量流速高于下游破碎系统所能处理的流量,从而导致堵塞和随后的设备损坏。
操作员可以在系统过载时控制系统或自动运行系统,但任何更改都会影响系统的一端或另一端。
工程团队得出结论,需要进行分析来评估系统中的所有变量如何影响给料器的质量流量
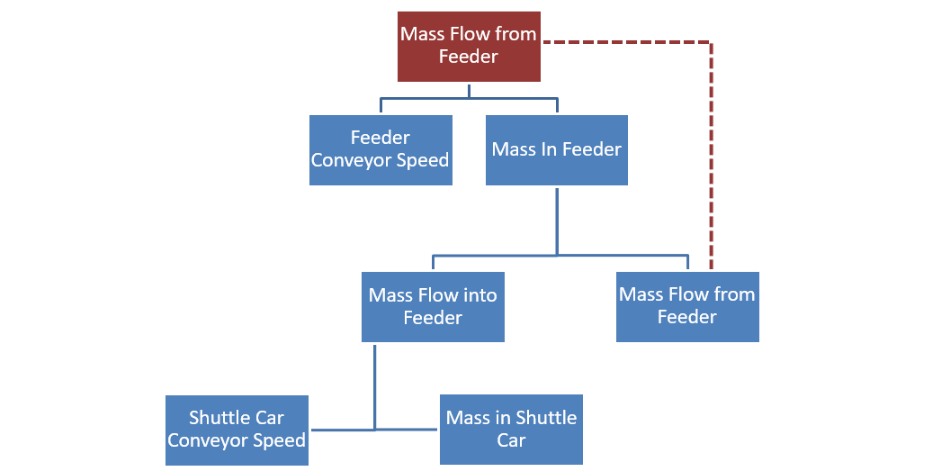
目标是优化所有协同工作的组件,并了解在发生溢出之前可以向下游进料多少材料。
研究的主要变量是给料输送机速度和原材料质量。仅 DEM 分析就需要很长时间才能运行,需要对每组输入进行新的求解。另一方面,ROM方法提供即时结果,最适合分析高度可变的系统。但是,它只提供了一个估计的答案。
3、最终方法
工程师们认为,最好的方法是系统数字孪生,使用Rocky DEM添加最终仿真进行验证。
该团队没有开发一次性减少订单模型,而是设置了两个单独的ROM(穿梭车和馈线)来处理所有变化:
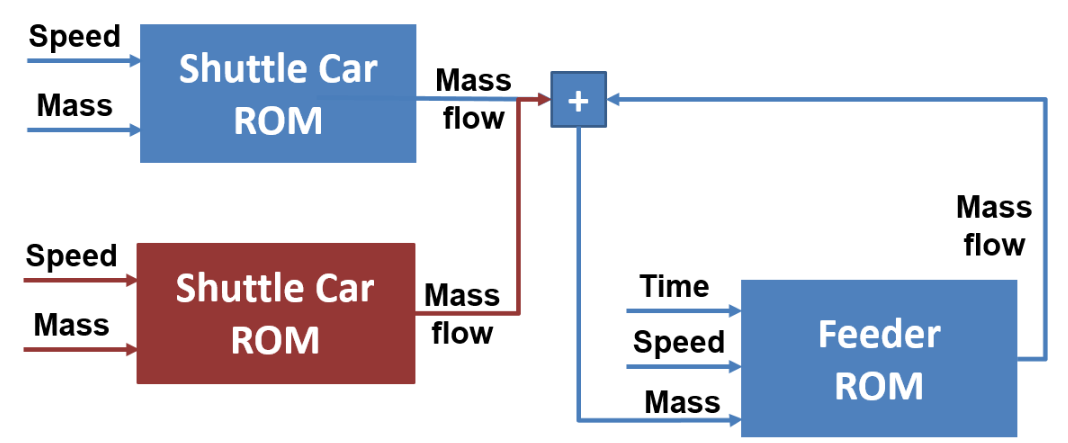
穿梭车测试用例设置涉及20吨原材料以不同的速度在输送机上运行。
该团队对穿梭车和馈线分别进行了四次模拟。这些仿真作为DesignXplorer的输入,跟踪几个时间点。

4、数字孪生验证
由于该团队无法在物理上记录运行中采矿过程中的数据,因此它对ROM模型中未包含的点运行了另一个Rocky DEM模拟,然后对两者进行了比较。
此 Rocky DEM 分析可作为现场测量的替身。验证案例涉及两辆20吨重的穿梭车,输送机速度为0.35米/秒;给料机输送机速度为0.46米/秒。
由于它是在Rocky中运行的,因此该给定点的数据是准确的(而不是估计值)。
将 Rocky DEM 结果与 Twin Builder 仿真进行比较,验证结果非常匹配,这表明使用这种技术构建降阶模型以及预测准确的现场结果是明智的。
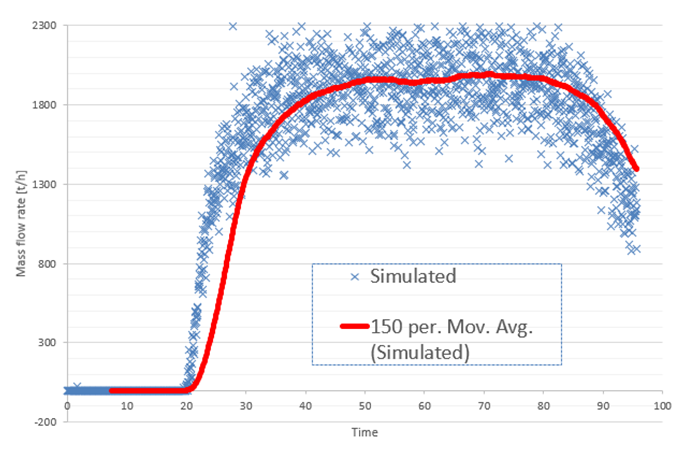
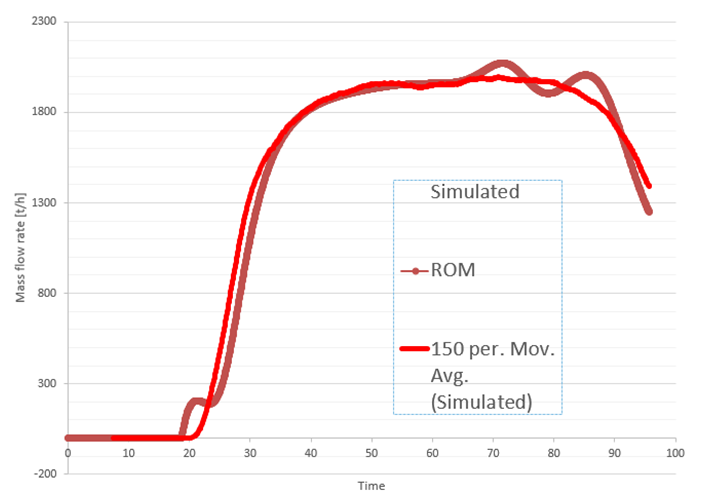
数字孪生体的好处远远超过所涉及的工作量。可能性包括:
- 链接到物联网平台以预测运营并避免不良后果
- 使用 ROM 可以立即查看变量对系统的影响,以便进行更明智的更改
- 修改ROM以包括溢出质量的计算
- 使用ROM优化系统
- 将ROM嵌入控制器(PLC),然后控制器可以自动实现输送机速度
可以想象,数字孪生具有巨大的潜力!
原文链接:A Digital Twin for the Bulk Materials Industry
BimAnt翻译整理,转载请标明出处